光伏行业深度研究之异质结电池专题报告
发布日期:2020-03-18 作者:创始人
发表于:2020-07-01 08:50:54
来源:未来智库
1. HIT 电池性能优异,商业化节奏提速1.1 HIT:一种非晶硅与晶硅材料相结合的高效电池技术
HIT 电池是以晶硅太阳能电池为衬底,以非晶硅薄膜为钝化层的电池结构。HIT(异质结电池,Heterojunction with Intrinsic Thin layer)是一种在 P 型氢化非晶硅和 n 型氢化非晶硅与 n 型硅衬底之间增加一层非掺杂(本征)氢化非晶硅薄膜的电池结构。标准晶体硅太阳能电池是一种同质结电池,即 PN 结是在同一种半导体材料上形成的,而异质结电池的 PN 结采用不同的半导体材料构成。日本三洋公司在 1990 年发明出 HIT 电池并申请为注册商标,因此异质结电池又被称为 HJT(Heterojunction Technology)或 SHJ(Silicon Heterojunction)。

HIT 电池与传统晶硅电池相比具有多种优势,具体体现在:
(1)转换效率高:HIT 电池采用非晶硅层降低表面悬挂键密度和异质结界面态密度,实现超高转换效率。HIT 电池的开路电压可以达到 740mV 以上,主要原因是:1)硅片表面的晶体结构具有不连续性,悬挂键密度高导致缺陷密度大,非晶硅层通过降低表面悬挂键的密度实现优良的界面钝化;2)HIT 电池在单晶硅衬底和掺杂非晶硅薄膜之间插入了一层较薄的本征非晶硅薄膜,使得异质结界面的界面态密度大幅度降低,因此电池的开路电压比常规电池高,进而实现超高转换效率。目前,HIT 电池的实验室效率在 26%以上,现有设施的平均量产效率在 23%以上,效率优势显著。
(2)双面率高:HIT 电池为正反面对称结构,且背面无金属背场阻挡光线进入,因此其天然具备双面发电能力,且双面率可超过 95%,可在扩展应用范围(沙地、雪地、水面等)的同时进一步提升发电量。
(3)无光衰:由于 HIT 电池上表面为 TCO,电荷不会在电池表面的 TCO 上产生极化现象,因此 HIT 电池无 PID、LePID 现象。松下 HIT 组件 25 年后发电量仅下降 8%。
(4)温度系数低,高温环境发电量高:HIT 电池的温度稳定性好,与单晶硅电池-0.42%/℃的温度系数相比,HIT 电池的温度系数可达到-0.25%/℃,使得电池即使在光照升温情况下仍有好的输出。在一天的中午时分,HIT 电池的发电量比一般晶体硅太阳电池高出 8-10%,双玻 HIT 组件的发电量高出 20%以上,具有更高的用户附加值。
(5)弱光响应高:理论研究表明,并联电阻越大,光伏组件的弱光响应越强。薄膜电池因为并联电阻普遍比较大,所以弱光响应普遍比较好。HIT 电池属于薄膜电池,因此弱光响应性能更好。
(6)工艺步骤少:HIT 电池生产工序仅需 4 步,量产具备优势。目前,主流的 PERC电池量产需要 8-10 道工序,TOPCon 需要 11-12 道工序,而 HIT 电池的工序仅为 4 道。从理论上讲,HIT 工艺步骤少,可以极大的降低电池的不良率,以及人工、运维等其他生产成本。
(7)结构对称,薄片化潜力大:HIT 电池完美的对称结构和低温度工艺使其非常适于薄片化。目前 PERC 电池所用硅片主流厚度为 170-180μm,HIT 电池所用硅片厚度已经降至 160μm 以下,且具有较大的薄片化空间。
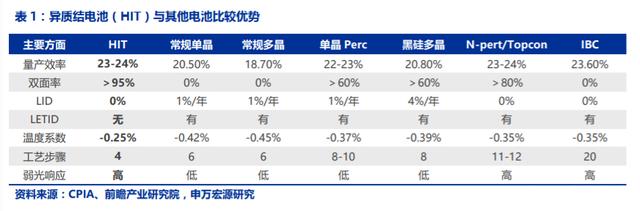
1.2 商业化节奏提速,多家公司进入
HIT 领域HIT 技术的发展可以划分为四个主要阶段,高效化趋势推动 HIT 商业化提速:
(1)起步阶段(1974-1996 年):HIT 技术初见雏形,日本三洋取得重大突破。1974年,Walter Fuhs 首次提出结合非晶硅和晶硅材料的 HIT 结构;日本三洋于 1989 年通过将本征非晶硅插入硅片和掺杂的非晶硅层之间取得重大突破,并将该技术申请专利;又于1990 年通过用非晶硅薄膜代替本征非晶硅,将 HIT 电池转换效率进一步提升至 15%。
(2)初步发展阶段(1997-2009 年):日本三洋注册 HIT 商标,各国相继启动 HIT技术研究。1997 年,日本三洋将 HIT 注册商标并提供该品牌异质结组件,硅片尺寸 5 英寸,电池效率 16.4%,组件效率 14.4%。2008 年、2009 年,瑞士梅耶博格、法国 CEA/INES相继建立 HIT 研发中心。
(3)工业化阶段:(2010-2017 年):日本松下(收购日本三洋)HIT 专利到期,HIT 进入快速发展的工业化阶段。2010 年,松下 HIT 专利保护到期,自此 HIT 技术迎来快速发展期。松下于 2013-2014 年连续创下 24.7%、25.6%的世界纪录。日本 Keneka 也紧跟其后,于 2016 年创造 BC-HIT 路径 26.6%的世界纪录。
(4)商业化阶段(2017 年之后):商业化节奏提速,多家公司进入 HIT 领域。2017年开始,全球多家公司开始关注 HIT 电池技术,中国晋能公司中试线规模达到 100MW。2018 年,中国钧石能源 HIT 电池/组件产线产能超过 600MW;ENEL 在意大利建设超过200MW 的产线。
多家厂商布局 HIT 产能,2020 年有望成为 HIT 产业化元年。量产方面,目前参与的厂商主要是:1)电池片环节新进入者;2)设备厂商;3)原有的薄膜电池制造商。当前全球 HIT 已有产能约 3GW,参与方规划 HIT 产能超过 15GW,部分企业已开始中试或小批量投运。钧石能源、中智电力、晋能科技、汉能等国内 HIT 技术领先企业已分别建成600MW、160MW、100MW、120MW 异质结电池产能。多家公司发布 HIT 产能规划,钧石能源、爱康科技分别规划建设 5GW 异质结制造基地,东方日升规划产能 2.5GW,中智电力规划产能 1.2GW。预计 2020 年将有 4-7GW 以上的 HIT 新增产能投放,一批标杆企业与项目可能在年底到明年投运,将进一步提升行业对异质结电池的信心,2020 年可能是 HIT 的产业化元年。
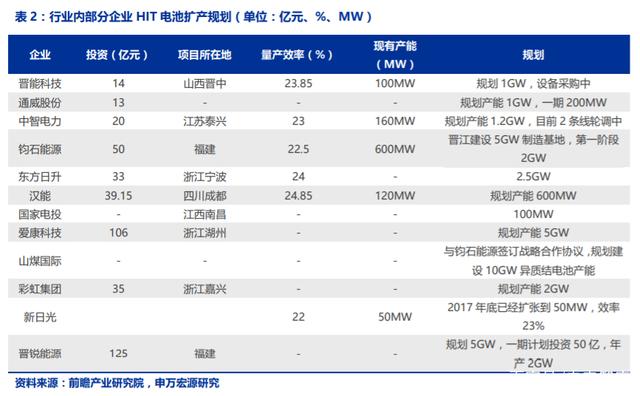
2. 转换效率提升空间大,HIT 有望成为下一代主流技术
2.1 “补贴退出+政策引导”推动电池技术向高效化迭代
平价上网渐近叠加补贴政策退出,降本增效成为光伏行业发展的主要推动力。“531”政策以来,我国光伏装机增速大幅下滑,各环节价格剧烈下跌,技术进步带来的降本增效成为推动平价上网目标实现的主要推动力。2019 年,我国一类、二类、三类地区,普通光伏地面电站标杆上午电价分别下降至 0.40、0.45、0.55 元/KWh,补贴幅度持续收窄。根据 CPIA 数据,2019 年,全投资模型下地面光伏电站在 1800 小时、1500 小时、1200 小时、1000 小时等效利用小时数的 LCOE 分别为 0.28、0.34、0.42、0.51 元/KWh。未来随着组件、逆变器等关键设备的效率提升,双面组件、跟踪支架等的使用,运维能力提高,2021 年后在部分高脱硫煤电价地区可优先实现与煤电同价。
电池片是光伏行业降本增效的关键环节,更高的转换效率可摊薄下游电站的面积相关成本。地面光伏系统投资中,组件价格占比 40.70%,而电池又占到组件成本构成的 67.5%,系统成本的下降主要依赖于组件价格及电池成本的下降。更高的转换效率可带来更高的发电增益率,单晶 P-PERC、中来股份 TOPCon、钧石能源异质结相比单晶 BSF 发电增益率分别为 3.0%、8.3%、11.0%。同时光伏电站的运输、安装、线缆、支架、运维、土地等成本均与面积成正相关关系,因此采用更高效的电池组件,可节省光伏电站面积,进而节约面积相关成本。

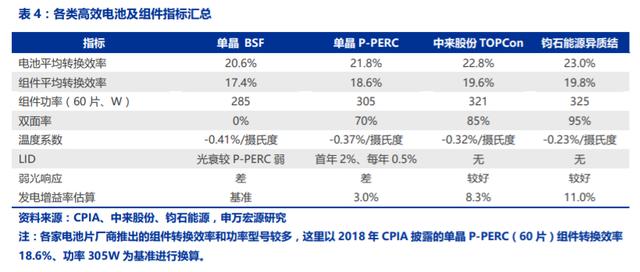
电池技术向高效路线进化:P-PERC 替代常规单晶,N 型技术路线繁多。历史上电池片环节经历了单晶替代多晶、P-PERC 替代常规单晶的技术迭代。其中常规单晶电池是铝背场电池,在硅片的背光面沉积一层铝膜;P-PERC 电池通过引入背钝化和开槽接触工艺,在电池背面形成背反射器,减少入射光损失,但背面开槽处金属接触区域增加额外的复合电流;N 型电池技术路线繁多,其中 N-PERT 是 P-PERC 技术的改进型,在形成钝化层基础上进行全面的扩散,加强钝化层效果;TOPCon 在电池表面制备一层超薄氧化硅和一层高掺杂多晶硅,氧化硅的化学钝化和多晶硅层的场钝化作用可以显著降低晶硅表面少子复合速率,同时超薄多晶硅层可保证多子的有效隧穿;HIT 通过引入非晶硅本征薄层来提升单晶硅的表面钝化性,使表面复合电流显著减小;IBC 把正负电极置于电池背面,减少置于正面的电极反射一部分入射光带来的阴影损失
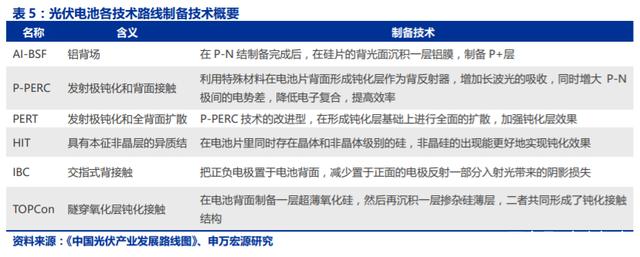
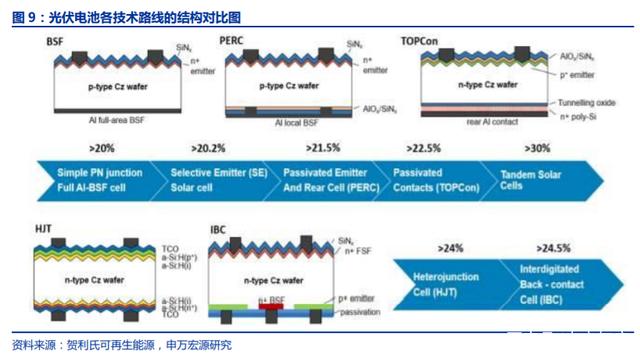
技术革新推动各技术路线电池转换效率不断提升。在《光伏制造行业规范条件》和“领跑者”计划推动下,各种晶硅电池生产技术进步迅速。2019 年,P-PERC 单晶电池效率提升至 22.3%,N-PERT+TOPCon 单晶电池、硅基异质结 N 型单晶电池平均转换效率分别已经达到 22.7%和 23.0%。预计至 2020 年,P-PERC 单晶、N-PERT+TOPCon、硅基异质结 N 型单晶电池的转换效率分别提升至 22.7%、23.3%、23.5%。
行业政策引导光伏制造企业高效化发展,利好高效电池技术导入。2020 年 5 月 29 日,工业和信息化部(电子信息司)对《光伏制造行业规范条件(2020 年本》(征求意见稿)进行公开征求意见。征求意见稿提出:电池制造项目投资强度不低于 900 万元/亩,组件制造项目投资强度不低于 500 万元/亩;现有项目多晶硅电池和单晶硅电池(双面电池按正面效率计算)的平均光电转换效率分别不低于 19%和 22.5%,新建和改扩建项目多晶硅电池和单晶硅电池(双面电池按正面效率计算)的平均光电转换效率分别不低于 20%和 23%。这意味着能够推动行业降本提效的新技术导入速度有望加快。
2.2 HIT 转换效率优势明显,有望替代 PERC 成为下一代主流技术

HIT电池量产转换效率具有明显优势,有望替代PERC 成为下一代主流技术。2019年,P-PERC 单晶电池效率提升至 22.3%,N-PERT+TOPCon 单晶电池、HIT 电池平均转换效率分别已经达到 22.7%和 23%。HIT 电池转换效率比 P-PERC 电池、N-PERT+TOPCon电池转换效率分别高出 0.7%、0.3%。预计至 2025 年 HIT 电池转换效率可提升至 25.5%,相比 P-PERC 电池、N-PERT+TOPCon 电池,转换效率高出 1.5%、1%。随着 HIT 技术大规模产业化,降本增效速度预期会大幅加快,HIT 有望替代 PERC 成为下一代主流技术。
目前 HIT 电池量产转换效率约 23%左右,实验室最高转换效率为 26.63%。松下收购三洋 HIT 电池产线后创下 24.7%的 HIT 转换效率记录,日本 Kaneka 公司通过在 HIT 电池中结合 IBC 电池结构,以 26.63%的效率水平创造了商用晶体硅太阳能电池的最高转换效率。但各家电池厂商的平均量产转换效率普遍在 23%~24%左右,其中松下量产转换效率为24.70%,钧石能源量产转换效率为 23.03%,晋能的 100MW 生产线平均转换效率为24.04%。虽然参与厂商较多,但各家 HIT 电池产能多在 500MW 以内、规模尚小。
2.3 可叠加其他高效电池技术,转换效率提升空间大
2.3.1 HBC:兼具 IBC 高短路电流+HIT 高开路电压优势
HBC(交指式背接触异质结)电池是结合异质结技术和背接触技术的电池结构。IBC电池正面为一层本征非晶硅薄膜钝化层,背面包含一层本征非晶硅薄膜及指状交叉分布的 P型氢化非晶硅和 N 型氢化非晶硅。与 HIT 电池结构相比,HBC 电池前表面无电极遮挡,并且采用 SiNx减反层取代 TCO 薄膜。
HBC 电池工艺流程为:清洗制绒-正面沉积本征非晶硅薄膜-正面沉积减反射膜-背面沉积本征非晶硅薄膜-背面沉积 P 型氢化非晶硅和 N 型氢化非晶硅-印刷烘干。
HBC 兼具 IBC 电池短路电流高和 HIT 电池开路电压高的特点,转换效率突破 26%。HBC 电池前表面无电极遮挡,可消除金属电极的遮光电流损失,保留了 IBC 电池短路电流高的特点;同时,HBC 采用钝化性能良好的本征氢化非晶硅层,降低了异质结界面的界面态密度,保留了 HIT 电池开路电压高的特点。2014 年 4 月,松下将 IBC 技术与 HIT 技术结合,在 143.7cm2 的 N 型 Cz 硅片上实现了 25.6%的转换效率。2017 年 8 月,Kaneka宣布将 HBC 电池转换效率提高至 26.63%。目前,国内各研究机构也致力于 HBC 太阳能电池的研究,中科院微电子研究所在 4cm2 的 N 型 Cz 硅上制备出了转换效率为 19.8%的HBC 电池,与国外研究成果相比仍有较大差距。
由于 IBC 电池和 HIT 电池产业化尚未成熟,而 HBC 电池在保留二者优势的同时也保留了工艺难度,目前 HBC 电池仍处在研发阶段。
2.3.2 钙钛矿/HIT 叠层电池:提升晶硅太阳能电池转换效率极限
晶硅太阳能电池实验室效率已接近极限,钙钛矿/晶硅叠层电池有望成为未来研发方向。光伏市场的 90%由晶硅太阳能电池所占据,目前实验室报道的晶硅电池效率最高已达到26.63%,在逐渐逼近其效率极限 29.3%。为使其超过这个极限,叠层电池是一种很好的策略,通常叠层器件分为两层,上层为宽带隙的材料,下层是窄带隙的材料。硅电池的带隙是 1.12eV,接近下层电池的最优带隙,因此需要匹配一个上层电池材料,其上层电池材料最优的带隙大约在 1.65-1.7eV 左右。考虑到光学损失及光致次带隙等各种因素,钙钛矿材料是优选的材料。
钙钛矿/晶硅叠层太阳能电池的工作原理是利用不同的带隙吸收不同的太阳光光谱,提高电池的转化效率。钙钛矿电池禁带宽度的调整范围为 1.5eV 左右至 1.7eV 以上,当钙钛矿的禁带宽度为 1.55eV 时,它可以吸收波长小于 800nm 的光子,而带隙为 1.12eV 的硅电池可吸收波长小于 1100nm 的光子。将钙钛矿电池与硅电池按能隙从大到小的顺序从外向里叠合起来,让短波长的光被最外侧的宽带隙钙钛矿太阳能电池吸收,波长较长的光能够透射进去让窄带隙的硅太阳能电池吸收,这就有可能最大限度地将光能变成电能,大大地提高了太阳光谱的利用率、电池的性能和稳定性。

TOPCon、IBC 电池正面采用 SiNx 钝化膜难以实现隧穿,HIT 电池是底电池的更优选择。理论上底电池可以采用 P 型电池或 N 型电池,但都需要在顶电池形成隧穿结以及一层(导电)光学层。底电池正面无需镀减反射膜,也无需金属化。由于底电池不导电,因此不适合采用标准 SiNx 正面钝化工艺,可以选择晶硅/氧化铟锡异质结技术,或选择带 ITO覆盖层的多晶硅钝化接触作为光学元件。
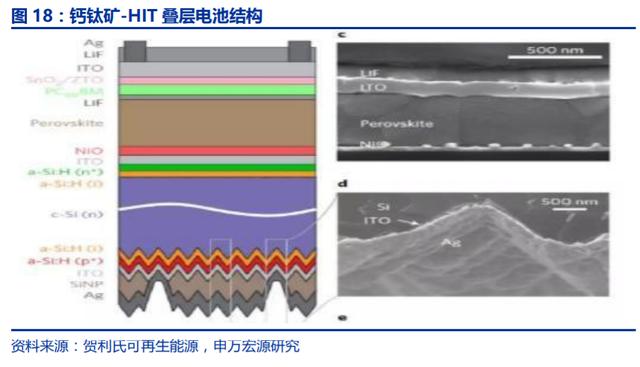
2017 年斯坦福大学研发出转换效率达到 23.6%的钙钛矿-HIT 双极太阳能电池。其中顶电池采用 CsFA 钙钛矿电池,具有 14.5%左右的转换效率;底电池搭配特制的 HIT 电池,为了适应层叠电池的需要进行了改造,光照面(和钙钛矿电池接触面)没有制绒,背面采用了制绒工艺并配合了局域金属接触实现最大吸光,具有 10%左右的转换效率。虽然钙钛矿电池和 HIT 电池为了配合层叠结构本身都做出了效率牺牲,但最后实现了 23.6%的超高效率。
牛津光伏制备出转换效率达到 28%的钙钛矿-硅串联太阳能电池,联手梅耶博格促进钙钛矿-HIT 叠层电池的规模化生产。2018 年 6 月,牛津光伏公司成功开发出效率高达 27.3%的钙钛矿/硅基双结叠层电池。2018 年底,牛津光伏公司的 1cm2 钙钛矿-硅串联太阳能电池达到 28%的转换效率。根据公司技术路线图,将来效率有望超过 30%。2019 年 3 月,梅耶博格与牛津光伏建立了战略性合作伙伴关系并签署了独家合作协议,将梅耶博格领先的 HIT 及智能网栅连接技术(SWCT)与牛津光伏的钙钛矿太阳能电池技术相结合,合作促进钙钛矿-HIT 叠层电池的规模化生产。梅耶博格将向牛津光伏出售一条 200MW 的异质结生产线用于钙钛矿电池的试生产,此生产线将于 2020 年底在牛津光伏工厂中试运行,试生产线转换效率的初始目标为 27%。
3. 工艺流程大幅简化,设备国产化速度加快
3.1 HIT 制备工艺仅需四步,非晶硅/TCO 薄膜沉积设备壁垒较高
HIT 的工艺流程主要包括清洗制绒→电池正反面沉积本征非晶硅薄膜和掺杂非晶硅薄膜→电池正反面沉积 TCO 薄膜→印刷烘干。
制绒清洗环节:常用工艺为 RCA 清洗或臭氧(O3)清洗。本环节的目的是去除机械损伤层、降低表面反射率、提高表面清洁度。
非晶硅薄膜沉积:常用的工艺包括等离子体增强化学的气相沉积法(PECVD)与热丝化学气象沉积(HWCVD),其中本征非晶硅薄膜是 HIT 电池表面的钝化层,沉积后需要掺杂膜层来形成发射极和背表面场。
TCO 薄膜沉积:常用的工艺是磁控溅射(PVD)和反应等离子体沉积(RPD),沉积非晶硅薄膜后,通过 TCO 薄膜可以实现导电、减反射、保护非晶硅薄膜的作用。
电极金属化:通过丝网印刷在电池正背面印刷银浆制备电极,或通过无主栅/铜金属化技术实现电极金属化。
与 P-PERC、TOPCon 相比,HIT 生产工艺大大简化,因此具备较大的产业化潜力。P-PERC 工艺需要 8-10 道工序步骤,工艺难点在于氧化铝钝化、激光开孔问题,国内代表企业有乐叶、晶科能源、阿特斯、晶澳科技;N-TOPCON 工艺共有 11-12 道工序步骤,工艺难点在于硼扩散,多晶硅生产、掺杂,绕镀,国内代表企业有天合光能、中来股份、林洋能源、晶科能源;HIT 工艺只需 4 道工序步骤,工艺难点在于高效清洗和非晶硅制备,国内代表企业有汉能、晋能、中智、钧石能源、通威股份,其中在量产的有晋能、钧石能源。从理论上讲,HIT 工艺步骤少,可以极大的降低电池的不良率,以及人工、运维等其他生产成本。

HIT 电池产线所需设备包括制绒清洗设备→PECVD/HWCVD 设备沉积非晶硅薄膜→RPD/CVD 设备沉积 TCO 薄膜→丝网印刷设备→自动分选机。
非晶硅薄膜沉积设备和 TCO 薄膜沉积设备主要依赖进口,清洗制绒设备、电极金属化设备等环节国产厂商开始进入。清洗制绒设备目前以 YAC/Singulus 等国外设备为主,捷佳伟创已成功实现清洗制绒设备国产化。非晶硅薄膜沉积环节所需的 PECVD/HWCVD 设备技术壁垒较高,目前以 Ulvac/MB/AMAT/Jusung 等国外设备为主。TCO 薄膜沉积环节的 RPD/CVD 设备目前同样以国外设备为主,主要供货商包括 Sumitomo/MB/VonArdenne/AMAT/Jusung/精曜等。电极金属化环节迈为股份等国产设备厂商已有量产化应用,不过仍以海外设备为主。
HIT 电池产线设备投资额中非晶硅薄膜制备和 TCO 沉积设备成本占比接近 70%。以东方日升 2019 年发布的 2.5GW HIT 电池项目设备投资为例,HIT 电池产线设备投资额为10 亿元/GW,其中清洗制绒设备占比 8%,非晶硅薄膜沉积设备(采用 PECVD)占比 40%,正面和背面 TCO 沉积设备(采用 RPD)占比 28%,丝网印刷等后段设备合计占比 26%。
3.2 制绒、清洗:RCA/O3,YAC 为主要设备供应商
制绒清洗是 HIT 电池制作的首道工序。制绒清洗主要是利用强腐蚀性的化学制剂对硅片进行清洗和表面结构化,从而在表面制得金字塔状的突起。HIT 电池清洗制绒具体流程包括:预清洗→抛光→制绒→进行若干表面清洁步骤去除有机物和金属杂质(SC1、CP、SC2、DHF)。制绒清洗工艺的主要目的为:(1)降低硅片表面反射率,利用 KOH 腐蚀液对 N 型硅片进行各向异性腐蚀,即在硅片表面形成绒面,可将硅片表面反射率降低至 12.5%以下,从而产生更多的光生载流子;(2)形成洁净硅片表面,由于 HIT 电池中硅片衬底表面直接为异质结界面的一部分,故需形成洁净硅片表面,从而避免不洁净引进的缺陷和杂质而带来的结界面处载流子的复合。
制绒清洗环节存在 RCA 与 O3两种技术路线,目前业界多采用二者结合以平衡成本和制备效果。RCA 清洗通常使用碱性腐蚀液对硅片进行各向异性腐蚀,RCA 清洗获得的界面金属杂质较低,但是氨水会导致表面较为粗糙。由于 RCA 清洗化学品耗量较大且废液处理成本较高,目前行业内开始使用臭氧超纯水清洗代替 RCA 完成硅片制绒后清洗工作。臭氧的氧化还原势高于 H2O2,可有效去除金属、颗粒和有机物,而且不会增加硅片表面微粗糙度。臭氧清洗在满足工艺需求的同时,可降低化学品耗量及动力运行成本量,避免含氮废水的排放,更有发展前景。
YAC 为制绒清洗环节主要设备供应商,国内厂商积极进入实现国产化。目前 HIT 产线的清洗制绒设备以进口为主,主要国外设备厂商包括日本 YAC、德国 Singulus、德国 Rena等,其中 YAC 在 HIT 清洗制绒设备市场具有绝对竞争力。YAC 制绒清洗设备的主要优势包括:(1)YAC 的制绒清洗设备可以在较宽的 Si 浓度下(0%-4%)进行稳定的制绒(2-10μm);(2)高纯度的化学试剂也帮助 YAC 制作出质量更高的绒面。国内设备厂商方面,捷佳伟创 HIT 制绒清洗设备研发已基本完成,进入工艺验证阶段。捷佳伟创的制绒清洗设备产能达到 6000 片/小时,破片率≤0.05%,参数已接近国外厂商。
3.3 非晶硅膜沉积:PECVD/HWCVD,HIT 电池制备的核心环节
非晶硅薄膜沉积是 HIT 电池制备的核心工艺。该工艺主要是指利用 CVD 的方式来镀本征非晶硅层、P 型非晶硅层、N 型非晶硅层。因为 P-N 异质结是在 N 型晶硅衬底表面形成,并且沉积层决定钝化的效果,因此这一步骤是决定 HIT 电池性能的关键。现行的异质结非晶硅薄膜沉积主要有两种工艺方法:等离子体增强化学的气相沉积法(PECVD)与热丝化学气象沉积(HWCVD)。
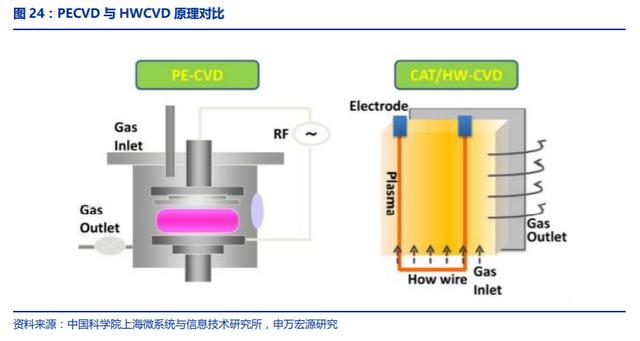
PECVD 是目前非晶硅薄膜沉积环节主流技术,工艺成熟度较高。PECVD 是指利用辉光放电的物理作用来激活化学气相沉积反应的 CVD 技术。PECVD 产生等离子体的过程为反应提供所需的大量能量,从而显著降低沉积反应温度,使得 CVD 过程得以低温下实现,降低了能源消耗,有利于生产成本降低。薄膜光敏性高、隙态密度低、且没有尺寸限制是PECVD 方法制备 a-Si:H 薄膜的三个重要优点。加之 PECVD 的低温工艺使得对制备薄膜时衬底要求不高,大大扩大了该方法的使用范围。
日本松下采用 HWCVD 法沉积非晶硅薄膜。HWCVD 以加热的方式赋予原料气体以能量使其发生各种化学反应,在基片上析出非挥发性的反应产物发生相变来制备薄膜。与PECVD 相比,HWCVD 的沉积不需要等离子体,是依靠分解硅烷来实现的。而且从热丝发射的电子能量很低,不存在 PECVD 中离子轰击,对沉积薄膜表面作用较小,有利于优质非晶硅薄膜的高速生长。松下采用 HWCVD 工艺沉积本征非晶硅与掺杂非晶硅,此类工艺优点是对界面轰击较小,薄膜质量较好,对硅片钝化较好,但是均匀性较差并且维护成本较高。
非晶硅薄膜沉积设备技术壁垒高,以进口为主、造价相对较高。HIT 非晶硅沉积 PECVD设备与常规产线 PECVD 镀膜设备结构完全不同,目前应用材料、梅耶博格、日本真空和理想能源等可以提供沉积环节核心设备 PECVD,但造价仍相对较高。目前采用 HWCVD 技术的设备厂商主要是日本真空。国内厂商方面,钧石能源凭借自身建立 600MW 产能的技术积累,开始为 HIT 电池厂商提供包括 PECVD 在内的关键沉积设备,理想能源、捷佳伟创、金辰股份、迈为股份等均在积极进行 PECVD 设备研发。
3.4 TCO 膜沉积:PVD/RPD,短期内 PVD 是主流
TCO 薄膜主要是用作减反射层和横向运输载流子至电极的导电层。目前常用的制备方法是 PVD 和 RPD:传统 PVD 技术运用 SPUTTER 磁控溅射,使用 ITO(氧化铟锡)靶材;RPD 技术利用特定的磁场控制 Ar 等离子体的形状,从而产生稳定、均匀、高密度的等离子体,使用 IWO(氧化铟掺钨)靶材。
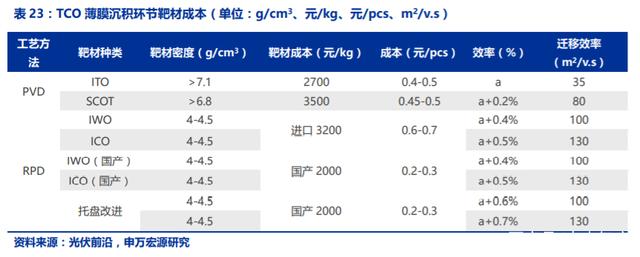
短期内 TCO 薄膜沉积的主流技术是 PVD,设备产能高、镀膜工艺可控。PVD 方法基本原理是在电场和磁场作用下,使工艺气体 Ar 电离成 Ar+,形成等离子体,被加速的高能粒子(Ar+)获得高能量并轰击靶材,靶材表面的原子脱离原晶格而逸出,溅射粒子沉积到衬底表面与氧原子发生反应而生成氧化物薄膜。PVD 溅射镀膜膜厚均匀易控制,镀膜工艺稳定可控,工艺重复性较好,靶材寿命较长,适合连续生产。但离子轰击对薄膜的性能损伤较大,转换效率相对较低。现阶段采用 PVD 方式成膜的企业较多,PVD 设备更为稳定且价格更为便宜,产能可以做到6000pcs以上,德国冯阿登纳公司已经推出产能 8000pcs设备。
RPD 设备和靶材受专利限制,但转换效率具备优势。RPD 镀膜原理是 Ar 通过等离子枪产生的等离子体进入到工艺腔体内,然后在磁场作用下打到靶材上,靶材升华沉积至衬底上。RPD 工艺主要是采用日本住友的 RPD 设备匹配其生产的 IWO 靶材,相对于传统 PVD工艺,RPD 工艺在转换效率上具有 0.3%-1%的优势,日本松下公司的 1GW 电池均采用RPD 工艺。RPD 具有低离子损伤、低沉积温度、可大面积沉积和高生长速率等优势,但目前 RPD 设备产能较低导致售价高,且核心部件和靶材受制于住友专利限制。国内靶材公司已经开发出日本住友使用于 HIT 的高效靶材,靶材成本或将大幅下降。

3.5 电极金属化:丝网印刷/电镀铜,丝网印刷国产化程度高
电极金属化是 HIT 电池制备的关键环节之一。制备电极的目的是通过与硅形成具有良好导电性能和高电流收集效率的欧姆接触,收集光生载流子并导出到电池。金属化环节不但要保证与硅界面有高的粘结强度和低的接触电阻,同时要为电流输出提供高导通路,是决定电池光电转化效率和成本高低的主要影响因素之一。目前常见的 HIT 电池金属化技术包括丝网印刷、电镀铜。
丝网印刷技术是 HIT 电池电极金属化环节主流工艺,技术成熟度较高。丝网印刷是通过丝网印刷设备将浆料印刷至电池表面,浆料中的金属颗粒在高温条件下,表面熔融相互连接并刻蚀硅板,形成可靠的黏结和电学接触。目前,工业界普遍采用丝网印刷技术在电池基底材料上印刷电池栅线即金属电极。丝网印刷技术相对其他技术而言,首先其设备结构相对简单、价廉、易于操作;其次印刷工艺成熟、生产效率高,容易实现大规模的自动化生产,在一定程度上可以节约时间和成本。然而丝网印刷银浆制备的栅线电极存在电导小、高宽比小等缺陷,且银浆价格昂贵,限制了 HIT 电池转换效率的进一步提高和生产成本的下降。
电镀铜技术利用电化学方法制备金属电极,可降低 HIT 电池成本、提升电池效率。电镀技术是利用电化学方法在导电固体表面沉积一层薄金属、合金或复合材料的过程。电镀溶液在通电后金属阳离子受电位差作用而移动到电池表面,沉积形成金属镀层,这层金属镀层即电极。选用电镀技术制备金属栅线电极,使用含银的电镀液,选择镍/铜/银三镀层,或者用镍/铜镀层,通过降低银含量使得电池成本具有竞争力。电镀铜电极具有导电率与银相当、接触电阻优于银胶的优点,并且采用低温制程技术,进一步缩小了电极线宽、增加了光照面积,有望提升 0.2%以上的电池绝对效率。电镀金属电极工艺过程较为复杂,附着力不良,存在废液对环境污染的风险,因此当前市场份额还很小。
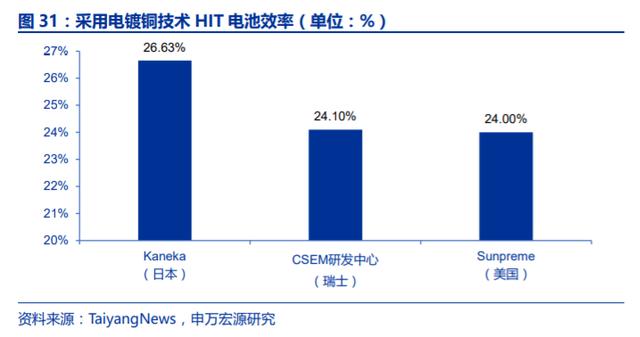
目前异质结丝网印刷的供应商主要包括应用材料公司和日本的 Miro-tec 公司,国产的供应商包括迈为股份、科隆威等。应用材料公司一直是该技术和市场的领导者,推出多项领先技术:细线二次印刷技术,可提高电池效率、降低浆料损耗;SoftPressure 技术,可将网板的寿命提高 20%以上,而且让印刷的质量更好。Micro-tec 丝网印刷的主要原理是通过空气平衡的方法来控制刮刀的压力来进行印刷。烘干采用 Wikettype 结构,在满足烘干时间的前提下,达到较高的产能。国产厂商方面,迈为股份率先打破国外厂商对丝网印刷设备的垄断,是国内市占率最高的丝网印刷设备厂商。
铜栅路线大幅降低银浆用量,钧石能源在相关工艺和设备已有产业化布局。目前钧石能源已经在开发电镀铜工艺并自主研发铜电极电镀设备,2018 年建造了一条基于铜电极技术的 500MW 生产线。电镀铜制备栅线电极是先在 ITO 表面采用 PVD 沉积一层种子铜,再图形化,然后再电镀铜和锡而成。这种方法制得的电池栅线电极界面结合力强,更加稳定可靠;电导比银栅高 3 倍;且铜材料成本低,既提高了转换效率,又降低了电池制造成本。

4. 浆料环节成本下降空间大,低温银浆、靶材技术壁垒较高
4.1 低温银浆、靶材在浆料成本中占比较高
清洗制绒环节和非晶硅沉积环节材料成本较低。目前清洗制绒环节,臭氧+双氧水工艺在大批量生产验证后清洗效果较为稳定,并且在去除氨氮工艺后污水处理与化学品成本大大降低,是现在最佳的清洗工艺,其总体化学品成本已经贴近 P-PERC 电池清洗成本,材料成本约 0.22~0.3 元/片。非晶硅沉积环节,射频化学气相沉积(PECVD 工艺的一种)的材料成本约 0.03~0.04 元/片。
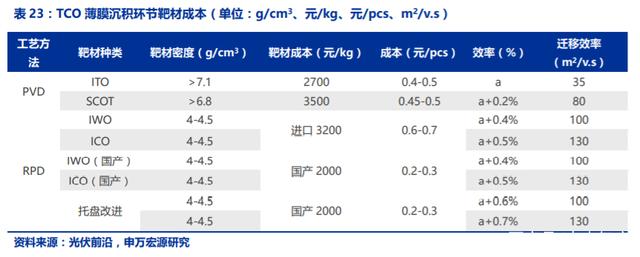
TCO 薄膜沉积环节:IWO 靶材成本高于 ITO,国产靶材降本空间大。对于 PVD 设备结合 ITO 靶材的工艺,靶材密度大于 7.1g/cm3,靶材成本约为 2700 元/kg,电池片的靶材成本约 0.4~0.5 元/片。对于 RPD 设备结合 IWO 靶材的工艺,进口 IWO 的靶材密度约4~4.5g/cm3,靶材成本约为 3200 元/kg,电池片的靶材成本约 0.6~0.7 元/片;若使用国产 IWO 靶材,靶材成本可降至 2000 元/kg,电池片的靶材成本约 0.2~0.3 元/片。
低温银浆是丝网印刷工艺所采用的关键材料,银浆用量大、成本高昂。传统晶硅电池通常采用高温银浆,导电性能较好。而 HIT 电池采用低温工艺,须使用低温导电银浆。由于低温导电浆料的导电性比高温导电浆料差,印刷性能也差,使得异质结电池的浆料增重较大,在四,五根主栅的情况下,大约在 300mg 左右,占据整个异质结加工电池的成本的约 30~40%。目前低温银浆主要采用日本京都电子生产的浆料,价格高昂,制造成本为 0.08美元/W,而 P-PERC 高温银浆的相应成本不到 0.02 美元/W。
4.2 低温银浆:国产化及电极工艺进步是降本关键
低温银浆工艺技术要求高,配方、三辊工序是关键工序。低温银浆的制备工艺共分为配料、混料、搅拌、三辊混合、过滤包装 5 大步骤,其中配料及三辊混合工序为关键工序。银浆是配方型产品,配方对低温银浆的生产至关重要。配方设计的难点在于:1、平衡降低电极线电阻和提升电极焊接附着力之间的技术矛盾;2、在降低电极线电阻的同时保证电极的长期可靠性、降低电极制造成本。三辊工序是银浆生产过程中影响产品粘度、细度、固体含量、流变性能的关键混合工序。HIT 银浆是低温固化型有机体系,对温湿度、有机及金属杂质的影响更加敏感,所以相比于高温光伏银浆在三辊工序,需提升剪切速度、温度、辊距控制精度。此外,高温银浆使用的 1-3μm 球形银粉无法在低温工艺中使用,专用银粉的开发也是 HIT 低温银浆技术开发的重点。
低温银浆尚依赖进口,国产供应商处于起步阶段。目前 HIT 银浆市场占有率最大的供应商是来自日本的 KE。日本 KE 专注 HIT 电池使用的低温银浆开发,目前其 Finger 细栅产品的体电阻率已低于 6*10-6Ωcm,并将在 1 年内通过引入低温烧结银粉技术,将电极体电阻率降至 4-5*10-6Ωcm;细栅产品可印刷 35-40μm 宽的 Finger 设计网版,该产品焊接拉力大于 1N/mm。日本 Nanotech、杜邦、贺利氏均有开发过 HIT 低温银浆产品,但目前面试的量产品市占比较小。国内供应商方面,目前已宣称涉足该领域的国内厂商有常州聚和、深圳首骋、苏州晶银、上海匡宇等 4-5 家。常州聚和生产的 CSP-T1 高效低温固化 HIT证明银浆在印刷性、体电阻率和焊接拉力方面均已接近进口产品同一水平。
MBB、SWCT 工艺可大幅降低银浆用量,系当前主要降本手段。多主栅(MBB)一般是指太阳电池有 5 根以上的主栅线,目前已应用于同质结太阳能电池。研究显示,多主栅技术在电池端转换效率可提升大约 0.2%,节省正银耗量 25-35%。该技术同样可应用于异质结太阳能电池,有效降低银浆使用量。采用 5BB 技术的 HIT 电池银浆单耗约为 300mg/片、银浆成本约 1.9~2.1 元/片,采用 MBB 技术的银浆成本约 1.1~1.2 元/片。梅耶博格采用的 SWCT 技术,将一层内嵌铜线的聚合物薄膜覆盖在异质结电池正面,代替银主栅,可降低银浆单耗至 100mg/片,银浆成本降至 0.6-0.7 元/片。

4.3 靶材:工艺技术要求高,初步实现国产化
TCO 薄膜制备主要采用 ITO、SCOT、IWO、ICO 四种靶材。溅射是制备薄膜材料的主要技术之一,它利用离子源产生的离子,在真空中经过加速聚集,而形成高速度能的离子束流,轰击固体表面,离子和固体表面原子发生动能交换,使固体表面的原子离开固体并沉积在基底表面,被轰击的固体是用溅射法沉积薄膜的原材籵,称为溅射靶材。TCO 薄膜沉积环节主要存在 PVD 与 RPD 两种技术路线,PVD 技术以 ITO/SCOT 作为靶材,RPD技术采用 IWO/ICO 作为靶材。

靶材制造工艺技术要求高,我国企业与国际先进水平尚有较大差距。靶材的质量水平会直接影响到沉积所得薄膜的均匀性和一致性,因此溅射靶材对纯度、致密度和组织均匀性等特性均有严格要求。太阳能电池等领域对金属纯度的要求一般为 99.995%(4N5);靶材的致密度会对溅射的沉积速率、溅射膜粒子的密度和放电现象以及薄膜的电学和光学性能有显著影响;靶材的成分、组织和晶粒度大小主要影响沉积薄膜的均匀性和质量的稳定性。烧结法是生产靶材的最优工艺,金属铟经过煅烧制成粉末,再和氧化锡或者氧化钨粉末按照一定比例混合,压块高温烧结制成靶材。2018 年的数据显示,日韩企业可以做出长 3000 毫米、宽 1200 毫米的单块靶材,但国内的长度不超过 800 毫米。

高端靶材市场被日韩企业垄断,ITO、IWO 靶材已初步实现国产化。国内金属的提纯技术有限,无法达到高纯溅射靶材的生产要求,因此,高纯溅射靶材上游的高纯金属市场目前也主要被日韩企业所垄断,日本三井、东曹、日立、三星、康宁等是全球 ITO 靶材主要供应商。国内在小尺寸溅射靶材制造水平上已达到国际先进水平,但大尺寸水平距离国际先进水平差距较大。国内先导、映日等企业 ITO 产品已经比较成熟,SCOT 正在积极研发,IWO 壹纳已经实现国产。广东先导的 ITO 靶材业务收购自优美科国际有限公司,其生产的高纯度、高密度 ITO 旋转和平面靶标,长度可达 4000 毫米。
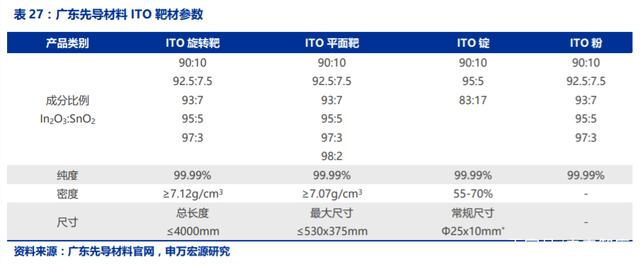
5. 多途径提升 HIT 经济性,2022 年 LCOE 有望与PERC 持平
5.1 产业化前期成本尚高,多途径降本提升 HIT 电池经济性
与 PERC 电池相比,HIT 电池银浆、靶材等材料成本及设备成本较高。PERC 电池技术相对成熟,产业化已具备规模,非硅成本下降空间较小,目前 PERC 电池非硅成本约 0.26元/W,占电池成本 39%,电池成本约为 0.76 元/W(含税)。HIT 电池尚处于规模化初期,设备及关键材料依赖进口,非硅成本存在较大下降空间。根据测算,HIT 电池银浆成本约为 0.14 元/W,占电池成本 15%;TCO 靶材成本约为 0.07 元/W,占比 7%;折旧成本约为 0.13 元/W,占电池成本 15%,HIT 电池总成本约为 0.89 元/W(不含税)、1.01 元/W(含税)。

硅片环节降本:HIT 电池更利于采用更薄的硅片,硅片薄片化推动硅片成本环节下降。目前主流 PERC 电池硅片厚度为 160μm-180μm,受限于技术和工艺要求,降低到 160μm 以下的难度较大,并且硅片变薄会导致转化效率的下降。HIT 电池完美的对称结构和低温度工艺使其非常适于薄片化,钧石能源已量产 HIT 电池产品硅片厚度为 150μm,相较于PERC 产品有所降低。日本三洋 2013 年研发出的 HIT 电池采用硅片厚度仅为 98μm,电池效率达 24.7%。随着硅片切割技术的发展,HIT 电池采用的硅片厚度将逐步下降,预计至2025 年可降至 100μm,硅片成本可下降至 0.25 元/W。
靶材环节降本:国产化是推动 HIT 电池非硅成本下降的重要手段。TCO 薄膜沉积环节存在 PVD 与 RPD 两种技术路线,量产工艺中 PVD 路线主要采用 ITO 靶材,RPD 路线主要采用 IWO 靶材。目前我国靶材尚依赖于进口,成本高昂,采用 ITO 靶材的电池片靶材成本约 0.07 元/W。国内先导、映日等厂商正在大力推进靶材国产化,在成本方面已具备一定优势。随着国产化的进一步推进,预计到 2025 年,靶材价格可下降至 2000 元/KG 左右,靶材成本可下降至 0.03 元/W 左右。
低温银浆环节降本:银浆单耗存在下降空间,国产化是降本关键。目前 HIT 电池银浆成本较高主要存在两方面的原因,一是由于 HIT 电池双面印刷且低温银浆导电性较弱,银浆耗量较高;二是低温银浆生产工艺要求较高,主要依赖进口。常规丝网印刷的 5BB HIT电池产品银浆单耗约为 300-400mg/片,是同类 PERC 产品的 3 倍左右。未来随着 MBB技术、SWCT、电镀铜等技术的应用,银浆单耗将大大下降。低温银浆国产化方面,国内厂商积极推进,常州聚合、苏州晶银等厂商研发较为顺利。未来随着技术工艺进一步成熟、下游需求的放量以及国产化的推进,低温银浆成本有望大大降低,预计有望从 2019 年的0.17 元/W 降至 2025 年的 0.06 元/W。
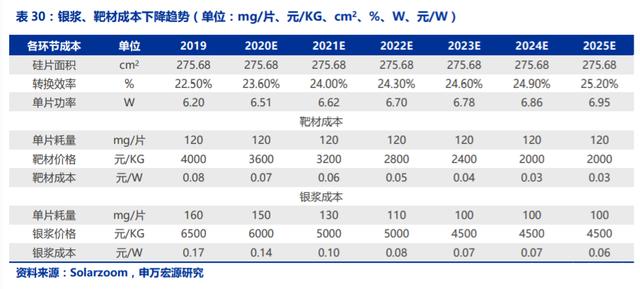
设备环节降本:关键设备国产化及设备产能提升推动成本下降。目前 HIT 电池产线单GW 投资成本约为 8 亿元/GW,需要各类设备约 10 台(套)/GW。所有环节中丝网印刷环节设备过程化程度最高,PEVCD、PVD 设备则主要依赖进口。目前国内企业包括捷佳伟创、迈为股份、理想能源等正在积极推进 PECVD 设备的国产化。未来随着设备国产化的推进以及单位设备产出的提升,单 GW 设备投资成本有望逐步下降,预计至 2022 年有望从目前的 8 亿元/GW 下降至 4.07 亿元/GW,至 2025 年预计可下降至 3.17 亿元/GW。
预计至 2025 年,HIT 电池成本有望从 1.06 元/W 下降至 0.57 元/W。综合各环节测算,未来通过 HIT 电池产业化规模提升、技术进步推动材料耗量下降及关键材料及设备的国产化等途径,HIT 电池成本将实现较大幅度的下降。2019 年,HIT 电池成本约为 1.06元/W,其中非硅成本 0.59 元/W。预计 2020-2022 年,HIT 电池成本可分别下降至 0.89元/W、0.78 元/W、0.72 元/W,相较 2019 年分别下降 15%、26%、31%;预计至 2025年,HIT 电池成本可下降至 0.57 元/W,相较 2019 年下降 46%。
HIT 组件成本随电池成本下降,转换效率提升摊薄 BOS 成本。HIT 电池转换效率更高,因此相比于 PERC 来说,对组件封装成本具有摊薄作用,随着 HIT 电池效率的持续提升,组件封装成本随之下降。HIT 电池成本下降叠加组件封装成本下降,推动 HIT 组件成本经济性逐步增强。我们预计到 2022 年,HIT 组件价格有望下降至 1.56 元/W(含税),到2025 年,组件价格有望下降至 1.28 元/W(含税)。
5.2 经济性快速提升,量产边际条件到来
预计至 2022 年,HIT 与 PERC 地面电站度电成本基本持平。HIT 与 PERC 相比,经济性主要来源于:(1)电池转换效率提升对 BOS 成本的节约;(2)低衰减、高双面率、低温度系数提升发电量。根据目前 PERC 与 HIT 组件价格,假设利用小时数为 1400 小时/年、项目年限 25 年、折现率 6%,PERC 与 HIT 电站 LCOE 分别为 0.289 元/KWh、0.300元/KWh。预计至 2022 年,当 HIT 电池成本降至 0.72 元/W,HIT 组件价格降至 1.56 元/W(含税)时,HIT 电站 LCOE 可降至 0.281 元/KWh,与 PERC 电站持平,从而具备落地经济性。